Dunwoody students rolled up their sleeves and spent the last several months designing and building three new autonomous snowplows from the ground up.
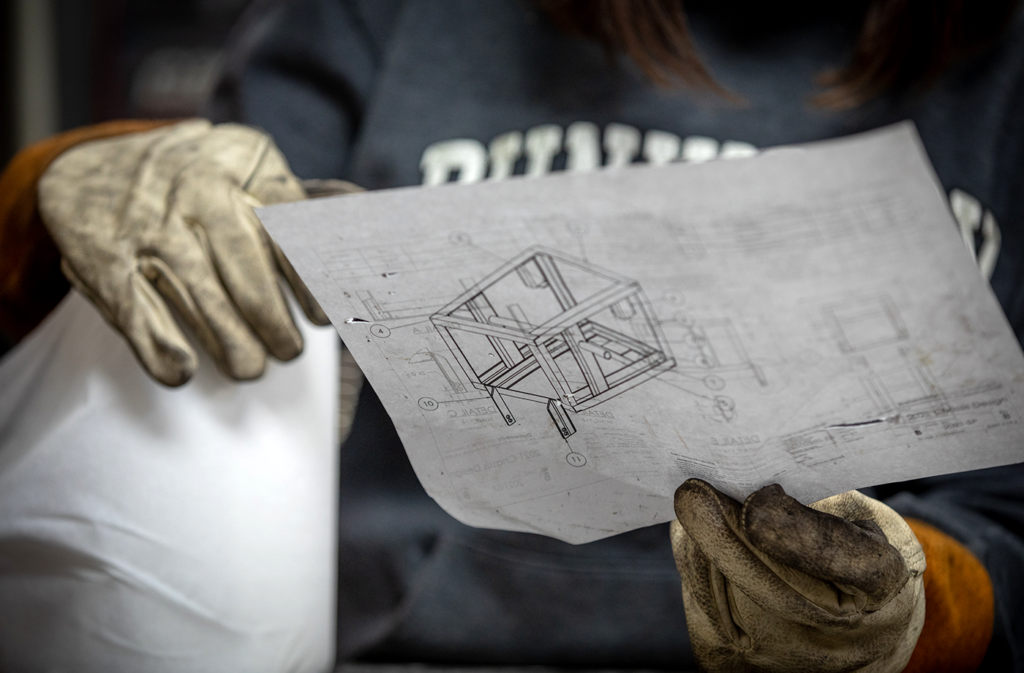
The new ones will update and replace namesakes Wendigo, Wechuge, and Snow Devil in the 12th Annual Autonomous Snowplow Competition, held on the Dunwoody campus later this month.
This type of upgrade is not an uncommon one for the Robotic Snowplow Team. Over the last 11 years Dunwoody students have built several platforms using various designs and parts; however, nothing was uniform with each of the robots.
This year’s team consisting of students from the Electronics Engineering Technology, Automation & Controls Engineering Technology, Automated Systems & Robotics, Welding, Machine Tool Technology, and Engineering Drafting & Design programs, took the best aspects of each of the previous designs and created a standardized chassis and parts for the three platforms.
“There are huge benefits to this standardization,” E.J. Daigle, Dean of Advanced Manufacturing, Robotics, Automotive Technology, Health Sciences, and Strategic Partnerships, as well as advisor for the College’s snowplow team said. “For example, we only need to stock one spare part for each component. If for some reason we have a failure, that part can go on any of the three robots.”
It’s a labor of love for the team members who typically spend their Monday afternoons and Saturdays on campus working on the robots.
Automated Systems & Robotics student Jessica Gugliuzza started out as the director of the chassis build and spent several days in the weld shop. “I have put in over 100 hours into this project, both in school and at home,” she said.
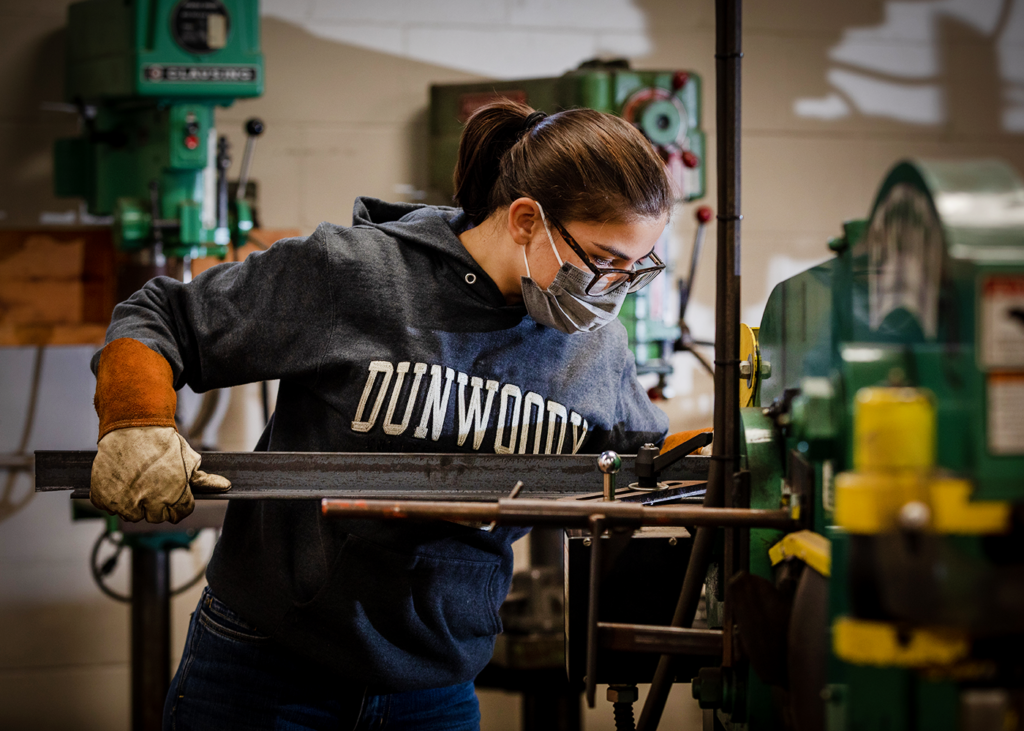
One Saturday morning in mid-November, a mixture of veteran and new team members gathered along with their advisors to assemble, paint, and work on the programming code needed to operate the snowplows.
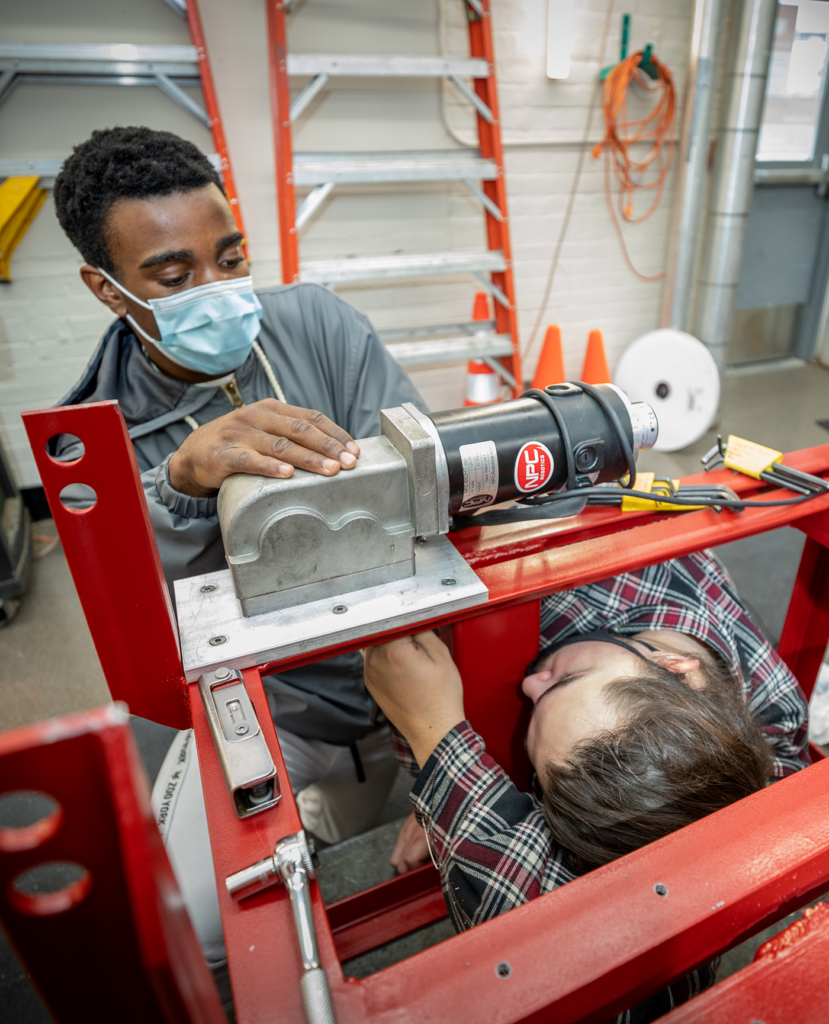
“This is my first year in the program so I’m learning how things work,” first-year Automated Systems & Robotics student Trougon Johnson said as he helped to assemble one of the plows. “The thing I’m looking forward to is seeing the other robots and how they are working out.”
Jim Jorgenson, ’11, Machine Tool Technology instructor, and alumnus of the original Snow Devil team as well as an advisor to this year’s team watched the team and was amazed at the advancements in the last decade.
The original Snow Devil, which Jorgenson helped build, was a lawnmower that had been modified into a plow by reversing the drive linkage, adding air power to engage the drive, and steering by counting wheel rotations.
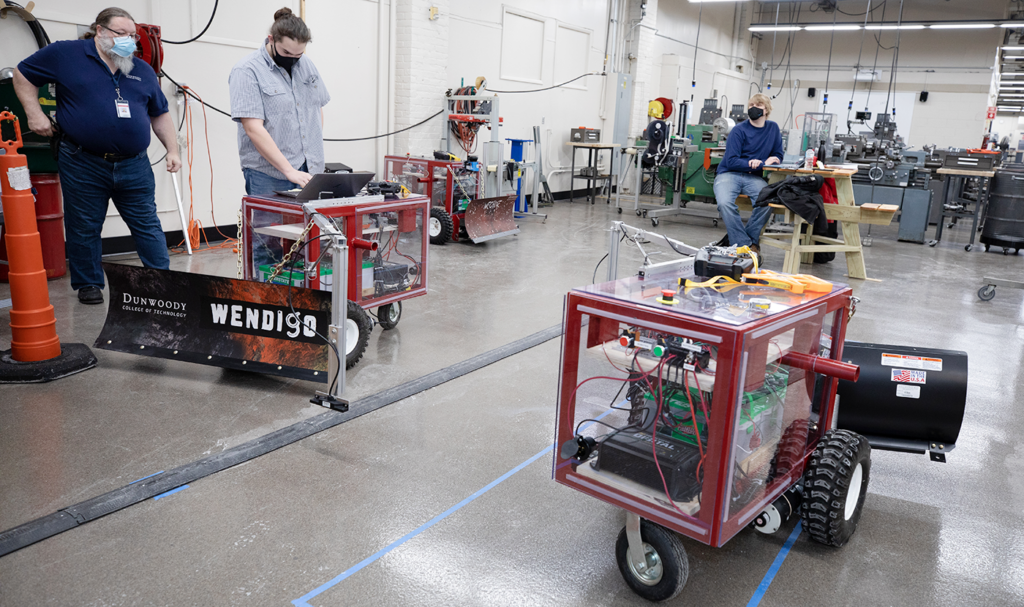
“We successfully built one robot,” Jorgenson said. “This year the students have created three robots based on a single chassis design. Three! They are electric, powerful, and innovative!”
While each of the robots may look the same regarding build, electronics, and mechanics, that is where the similarities end. The sensors and navigation strategies are all very different.
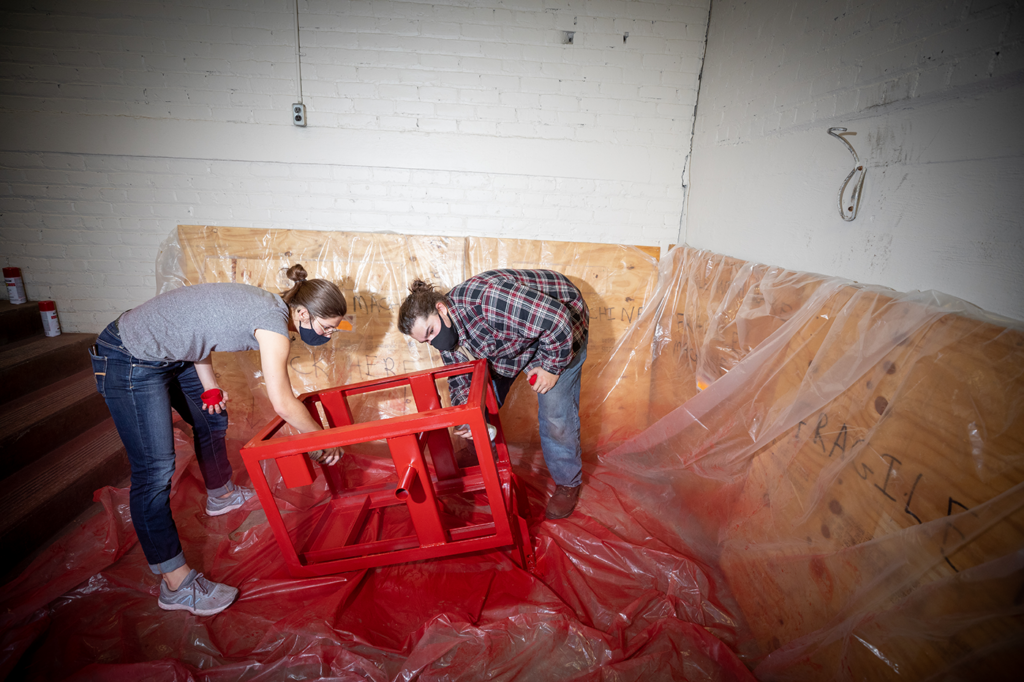
Wechuge is the most advanced platform. It uses a LIDAR system to map its surroundings to plan a path through the snowfield and will detect obstacles in its path. If an object is detected, it will then reroute to a new path.
It is this programming that Brenden Groff, a 2020 Electronics Engineering Technology alumnus and current Automation & Controls Engineering Technology student dove headfirst into.
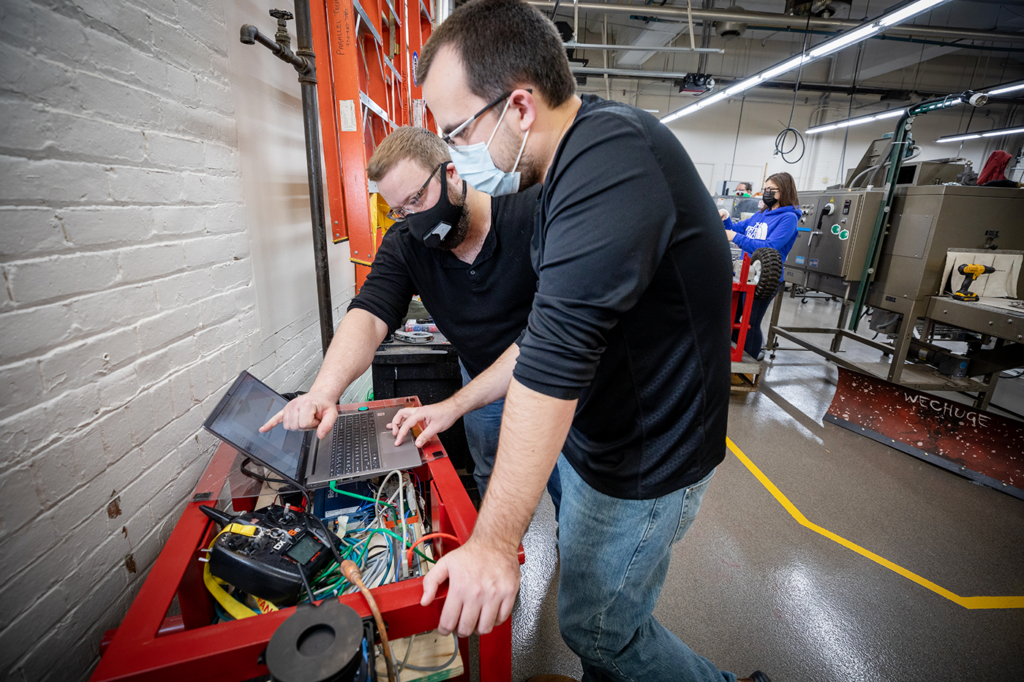
“There’s more to it than just knowing how to code in a certain language (Python, C++, etc.),” Groff said. “For this competition I’ve learned a lot about the basics of modern-day autonomous vehicles that range from understanding the basic principles, sensors, and algorithms autonomous vehicles use, to learning and understanding the software tools and practices that are used to make things happen.”
The other two platforms – Wendigo and the Snow Devil – rely on an infrastructure-based system where the plows navigate using a magnetic sensor and strip.
“This strip could be located at the edges of a driveway or sidewalk prior to winter,” Daigle said. “This is very similar to the technology used at Tesla to build vehicles at their Gigafactory.”
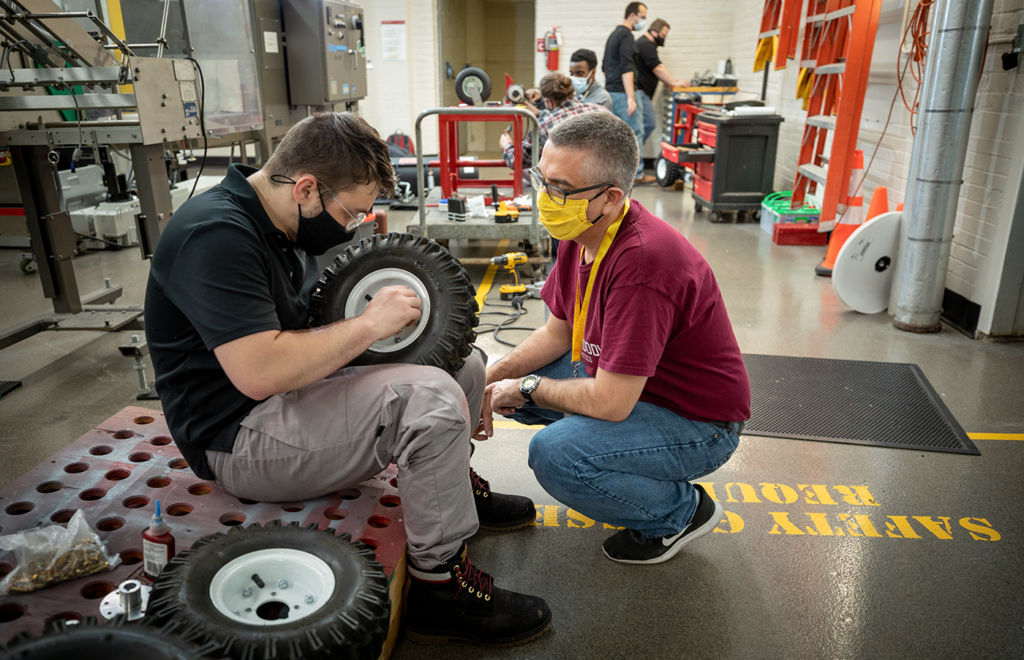
Dunwoody first hosted the Autonomous Snowplow Competition, sponsored by ION Satellite Division, on its Minneapolis campus in January 2020. Last year the competition was held virtually due to the COVID-19 pandemic.
Teams from Minnesota, Michigan, North Dakota, South Dakota, Ohio, and Quebec and Ontario, Canada will once again come together to battle against each other for bragging rights of having built the best snow-clearing robot on January 20-22, 2022, at Dunwoody.
While competitive spirit is abundant among the contestants, collaboration, and shared knowledge is another key element garnered from the event.
“Now that the three new chassis are built, I’ll be the leader for one of the three robots: Snow Devil,”said Gugliuzza, who competed virtually last year. “It will be my first time seeing the competition play out in person, and I’m looking forward to meeting all of the other teams.”
Groff joined the Robotic Snow Plow team during his second semester in 2019, and was able to participate in the first snowplow competition held on campus. He is especially looking forward to the return to the in-person format.
As in year’s past, there will be two categories of competition: the single 1 and a triple 1. During the single competition, which is a 1 x10 meter-long snowfield, each team competes individually. During the triple competition, each team must collaborate with another plow to clear the 3×10 meter-long snowfield.
“Collaboration could mean anything from the snowplows communicating wirelessly with each other to using other sensors to communicate,” Groff said.
Teams Wendigo and Snow Devil are partnered for this task and will use reflective laser sensors to determine when one of the snowplows goes.
Team Wechuge, of which Groff is a member, is collaborating with Minnesota State University Mankato. “We plan on having the snowplows communicate their positions to each other wirelessly,” he said. “I’m most excited to see and learn what the other team’s solutions are for this competition.”