Dunwooody’s Supermileage team is making progress, but still has a ways to go
A team of School of Engineering students is hard at work this semester getting ready to compete in the SAE Supermileage competition, which takes place June 4-5 in Marshall, Michigan. The competition tests undergraduate and graduate students’ engineering design abilities and requires them to build a single-person, fuel-efficient vehicle with the goal of completing a specified course with the highest miles per gallon rating.
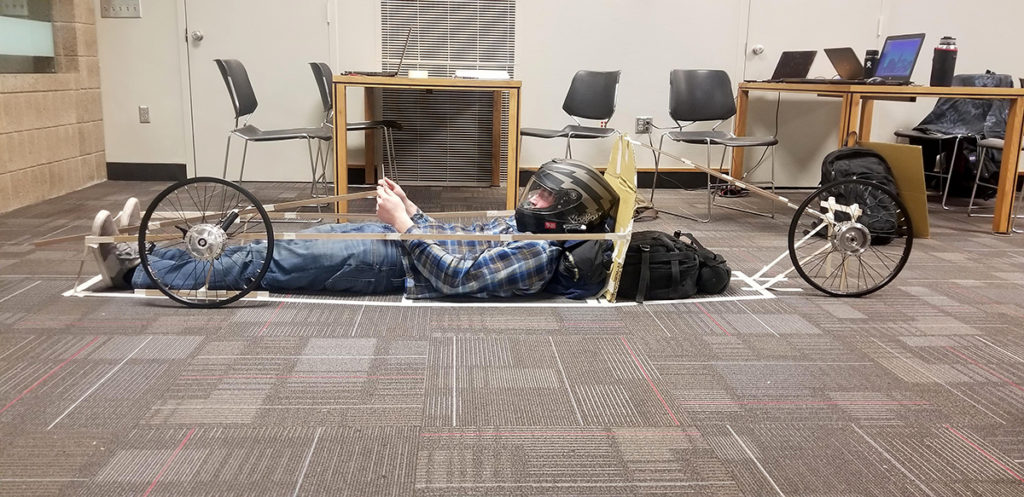
Last year’s competition featured 20 teams with an average of nine students per team. Most other colleges have entered the competition before — some for many years — which means they have existing vehicles they are currently modifying and optimizing for the competition.
This is Dunwoody’s first year in the competition.
“Not only do we have to make a car that’s fuel efficient, but we have to make a car from the ground up,” said team project manager Eric Frisbie. “So that’s where most of our challenges stem from right now.”
All five pioneering members of the team are seniors who will be part of the first-ever Mechanical Engineering graduating class this May.
THE PLAN
Last semester, they formulated a plan, created design drawings, and sourced materials. So far this semester, they’ve focused on constructing a frame out of aluminum tubes, to which they will then attach a metal skid plate with holes drilled in it to reduce weight.
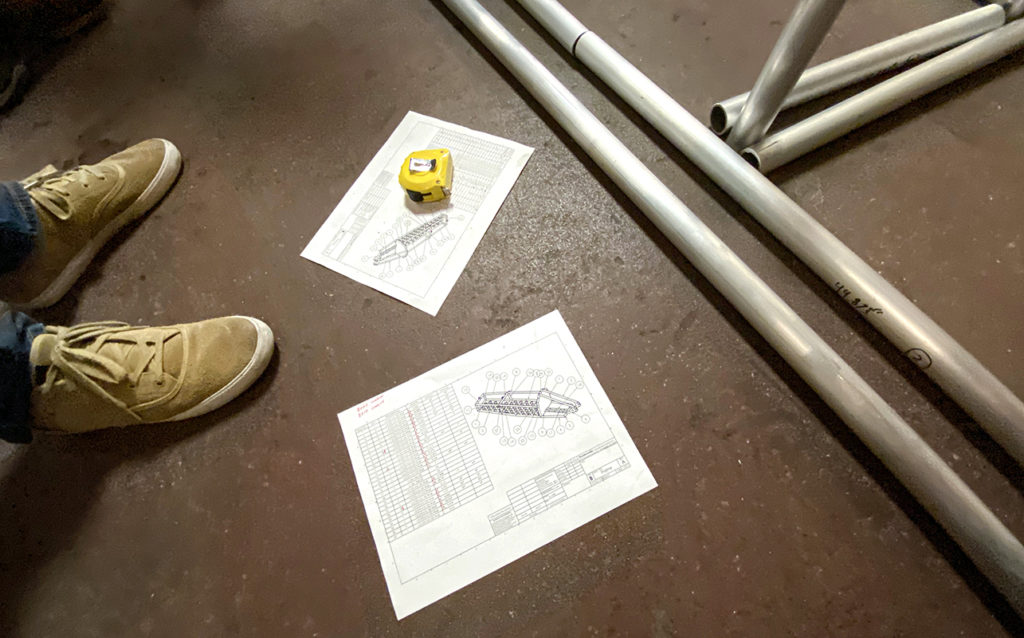
To construct the frame, the students have been spending a lot of time over in the Welding Program. Cutting the tubing using a metal saw went smoothly as it was a matter of measuring the various lengths, making the cuts, and then filing the end pieces smooth. Joining the tubing to create the frame is requiring more time and — learning additional skills.
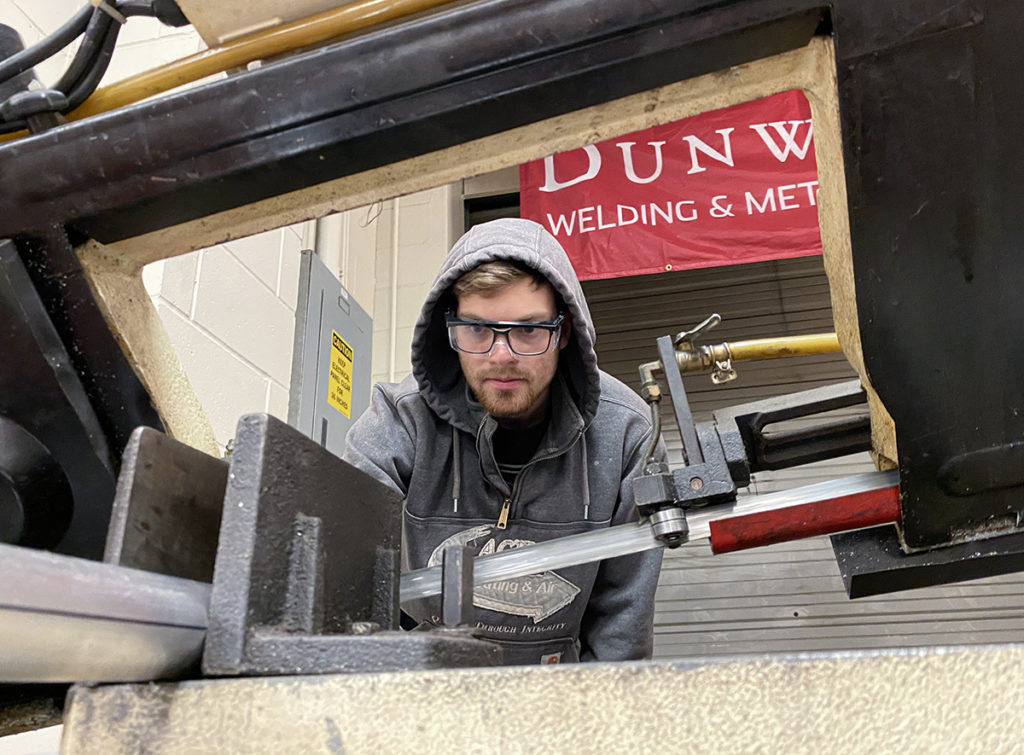
Three members of the team — George Ellis, Mike Rhode, and Micah Hovland — have put in practice time to hone their welding skills. Working with aluminum is tricky because it cools more quickly than steel and isn’t as strong. That means welds need to be steady and robust but quick so the welder doesn’t punch holes in the aluminum.
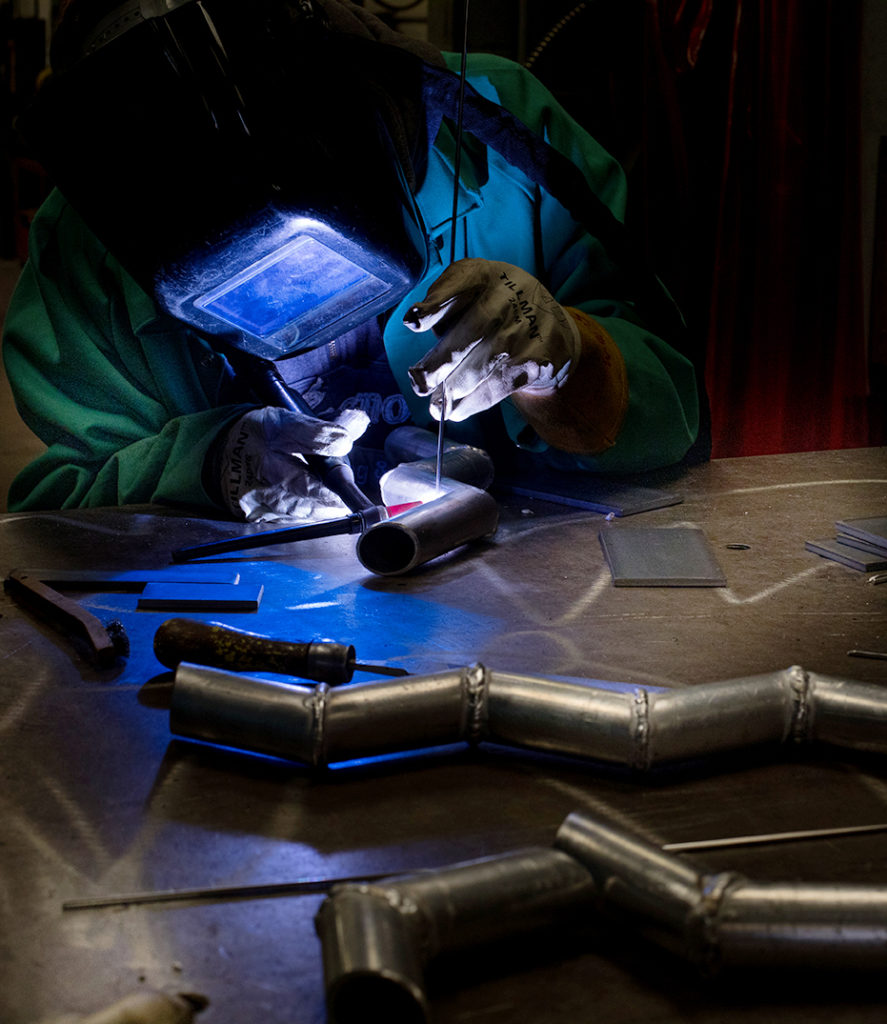
Even before welding could take place, the team needed to figure out how to cut the tubing so it would fit together. For that, they came up with a clever idea: they found a hole saw blade the same diameter as the tubing. This allows them to cut half-moon shapes into the end of one of the tubes so that it can then fit over another tube and be welded to it. The saw also lets them cut across tubing for diagonal joining.
While Ellis, Rhode, and Hovland work on the welding, the other members of the team, Frisbie and Matt Schafer have been spending time in the Machine Shop working on the rotors for the wheels.
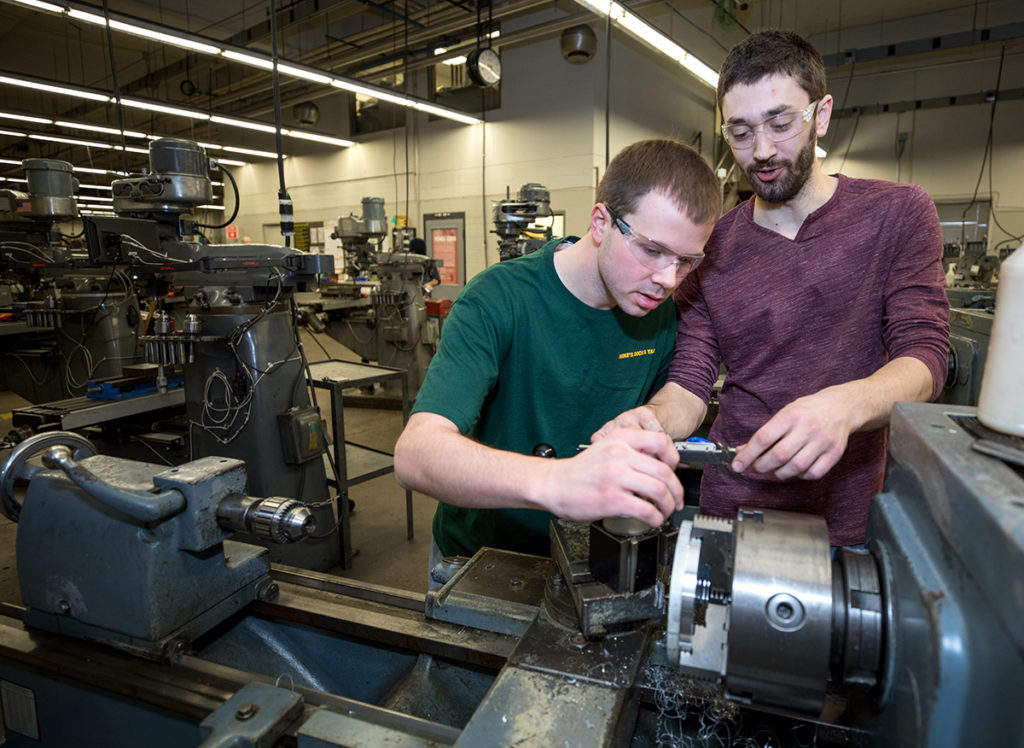
Once the frame is complete the team will shift their attention to the motor and fuel systems as well as the systems for steering, transmission, suspension, braking, and electrical — all the parts that make the vehicle start, stop, and maneuver. Finally, they’ll fabricate the outer shell of the vehicle, which will either be fiberglass or carbon fiber.
The team’s goal is to create a vehicle that will finish the race. And, more importantly, to build a solid platform so that future teams will be able refine and optimize the vehicle and compete for places and prizes. That’s what pioneers do.
Stay tuned to Dunwoody’s social channels for more on the progress of the Supermileage team: Instagram | Facebook | Twitter