Dream it. Design it. Build it. Refine It.
That is exactly what four senior Mechanical Engineering students did throughout their time at Dunwoody. Their capstone project was no exception.
Kurt Scepaniak owner of Horizon Roofing contacted Dunwoody with hopes that students in the Engineering Senior Design course would conceptualize and fabricate a machine that would make it easier to remove roofing material from horizontal roofs.
He explained that two-foot by two-foot sections of roofing material are removed and tossed into a tear off box on the roof’s surface. A crane removes the tear off box from the roof and typically needs to be emptied many times during the duration of the job.
“What our sponsor asked us to create was a machine that would reduce the size of the insulation sheets, so that it would take fewer lifts up and down with that tear off box,” Roy Heggernes, Mechanical Engineering ’21, said. “So that is what we built.”
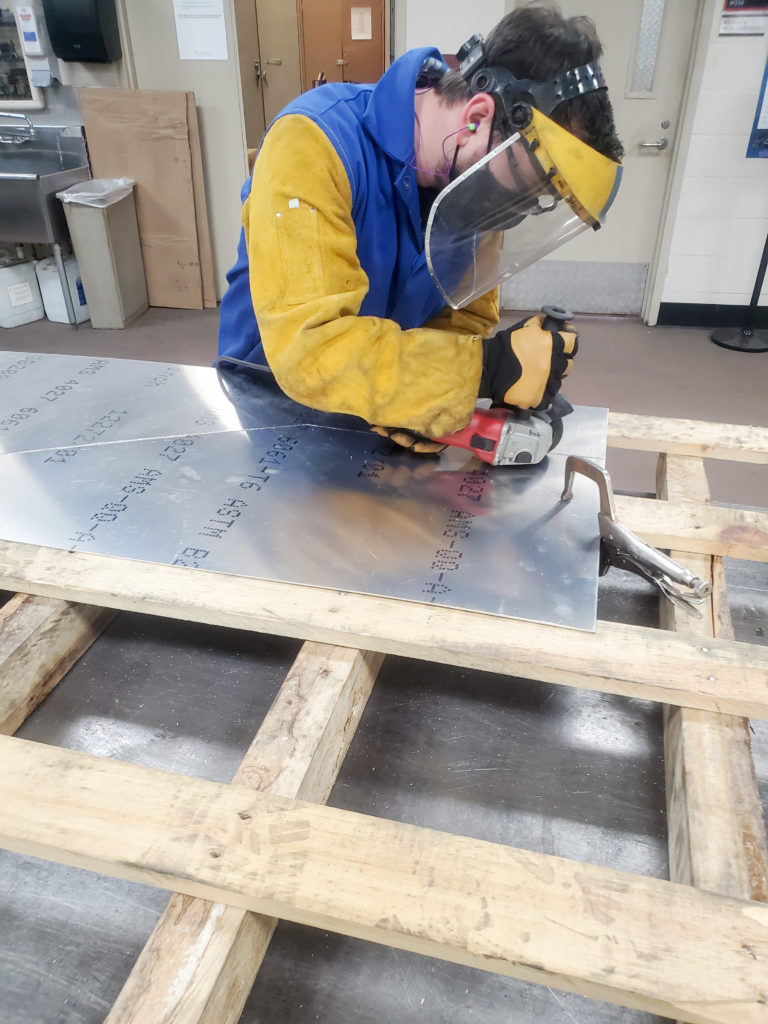
The Mechanical Engineering program, housed within the School of Engineering at Dunwoody, awards a Bachelor of Science degree upon completion. Classwork is project-based with theoretical engineering principles taught through hands-on experience and problem-solving. Two cohorts of classes have now graduated.
This project was a secondary phase of an idea that members of the first graduating section tackled — and had to abandon — when COVID-19 forced classes online in 2020.
When the class of 2021 returned to campus in the Fall, and agreed to the task, they were worried that it was a tall order — one they might not be able to deliver on.
“It was really challenging in the beginning,” Elizabeth Rivas, Mechanical Engineering ’21 said. “Trying to come up with the concept is sometimes the hardest part.”
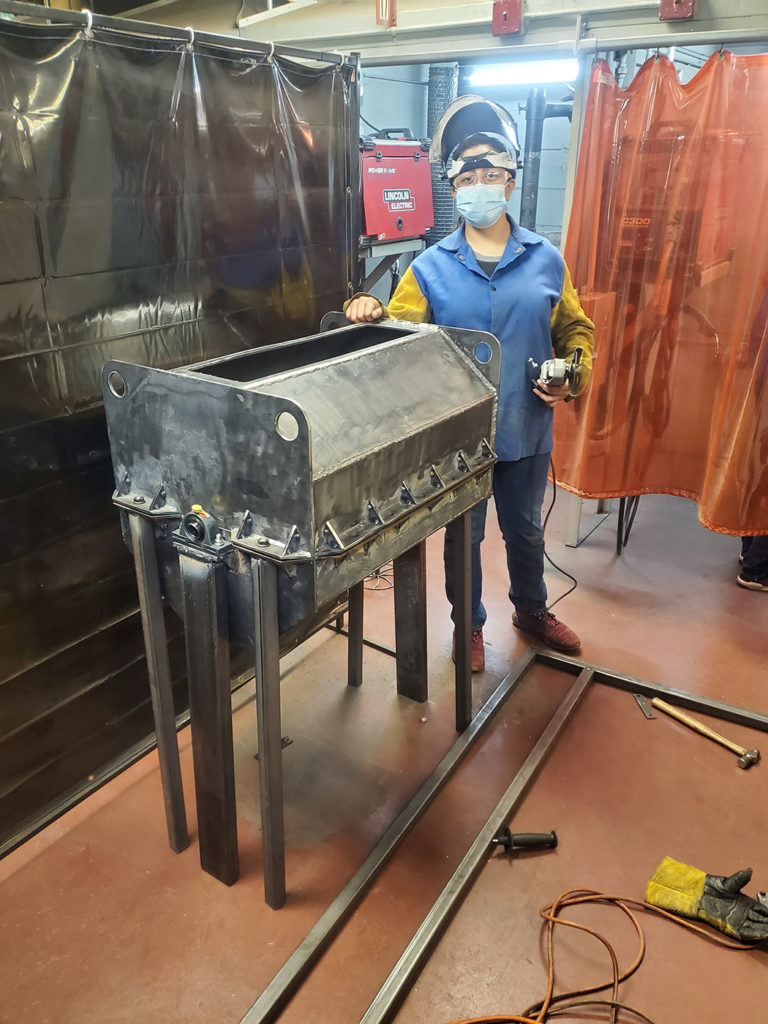
They spent much of the first semester brainstorming ideas while juggling other projects and classes.
By the second half of the semester, they had a concept drawn using a 3D CAD software called SOLIDWORKS.
“I started to see how this would be able to come together,” Rivas said.
“We were all kind of on edge, but once we actually got it going and started moving forward, we all gained an energy of ‘Hey! We can do this!’” Justin Grant, Mechanical Engineering ’21, said.
They codenamed their project “the cricket” after one of the initial whiteboard drawings resembled the insect that is considered a symbol of good luck in some cultures.
Dunwoody prides itself on small class sizes, and as a result students tend to develop close working relationships within their cohort.
Each member of the group credited their project’s success to their teamwork.
“It was really easy to split up tasks amongst each other,” Thomas Oldenburg, Mechanical Engineering ’21 said. “We kind of knew where each of us had our strengths and weaknesses.”
They approached each task as: “’We know you are the best one for this job, so we are going to put you on lead. If you need help, we’re here,’” he said.
Heggernes took the lead on the shell; Rivas, the frame; Oldenburg, the internal hammers, and Grant, the electrical parts.
Communication was also key.
“If one part was falling behind, we could all jump on it,” Grant said.
They also credited Dunwoody’s unique setting, housing other first-rate programs such as Machining and Welding, and cross-departmental collaboration with those faculty and students who helped guide them and even built some of the components for them based off their designs.
“We wouldn’t have been able to fabricate nearly as much on this project without their help,” Heggerness said.
Grant remembered sharing photos and videos of their progress with friends who were enrolled in engineering programs at larger universities. He says they were amazed at the scale of the project; their own experiences paled in comparison.
As the semester wound down, the students’ confidence increased.
“We tested the motor and all the wiring before hooking it up to the hammers,” Grant said. “It started up in about a half of a second, which was quicker than we expected.”
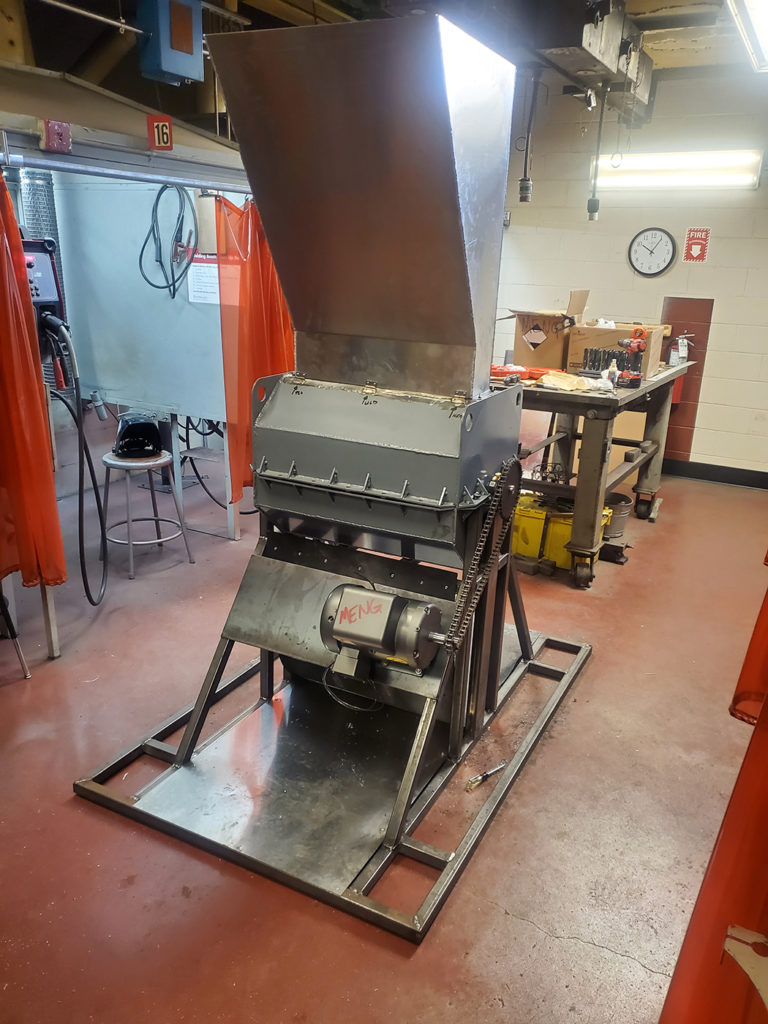
The machine, which has roughly a six-foot by four-foot footprint and an estimated weight of 600 pounds, was completely assembled by May 7, 2021, and along with it a sense of relief.
“When you first turn it on it has a sort of lawn mower or washing machine sound,” Oldenburg said. “And when you are feeding material through, it is just like a wood-chipper — you can hear the material impact; you can hear it grinding.”
Scepaniak, who has worked with Dunwoody and a couple other colleges on design projects, was on campus for the group’s presentation of their work.
“It is exciting to see,” he said. “This one is for sure the closest to a finished product I have seen yet.”
As he looked around the room filled with campus leaders and faculty who leant their expertise to the students, Scepaniak was amazed at the level of support.
“This is the most participation that I have seen with a student project,” Scepaniak said. “If my son wanted to go into engineering, this program is one that I would think highly of for my kid.”
One of those in the room who was filled with pride was Jonathan Aurand, PE, Associate Professor of Mechanical Engineering. He had the distinct opportunity of instructing the students during the past four years.
“They buckled down and put in the effort to realize the design they conceived and developed over several months,” he said. “The project sponsor was happy with the results and plans to further develop the initial prototype into a commercial product.”
Each of the members of the team was happy with their achievement and what they were able to accomplish.
“It goes to show that we can actually build something that we set out to design,” Heggernes said. “I feel like future employers will like that we went through the whole process of brainstorming ideas, coming up with a prototype, designing it, refining it, and then coming out with a final product at the end of it.”
Since then, each has graduated and gone on to accept jobs or continued with internships in their field of study. Rivas is a Digital Manufacturing Designer at ProtoLabs; Heggernes is a Quality Engineering Intern at Zeiss Industrial Metrology; Grant is a Manufacturing Engineer Intern at Lake Air Products; and Oldenburg is a Fabrication Engineer at Kurt Manufacturing.